The popular liquor vodka consists mainly of ethanol (ethyl alcohol) and water in roughly equal portions. Ethanol and water both have substantial vapor pressures, so both components contribute to the total pressure of the gas phase above the liquid in a closed container of the two liquids.
One might expect the vapor pressure of a solution of ethanol and water to be directly proportional to the sums of the values predicted by Raoult's law for the two liquids individually, but in general, this so-called "ideal" behavor is not observed. The reason for this can be understood if you recall that Raoult's law reflects a single effect: the smaller proportion of vaporizable molecules (and thus their reduced escaping tendency) when the liquid is diluted by an otherwise "inert" substance.
In a solution composed of two or more liquids, each of which has a measurable vapor pressure of its own, differences in the manner in which "like" and "unlike" molecules interact with each other make
"Ideal" solutions follow Raoult's law
There are some solutions whose components follow Raoult's law quite closely. An example of such a solution is one composed of hexane C6H14 and heptane C7H16. The total vapor pressure of this solution varies in a straight-line manner with the mole fraction composition of the mixture.
Raoult's law plot for a mixture of hexane and heptane.
Note that
- the mole fraction scales at the top and bottom run in opposite
directions, since by definition,
Xhexane = 1 – Xheptane. - Ptotal is the sum of the Raoult's law plots for the two pure compounds, indicating that this solution behaves ideally.
An ideal solution is one whose vapor pressure follows Raoult's law throughout its range of compositions.
Experience has shown solutions that approximate ideal behavior are composed of molecules having very similar structures. Thus hexane and heptane are both linear hydrocarbons that differ only by a single –CH2 group.
This provides a direct clue to the underlying cause of non-ideal behavior in solutions of volatile liquids. In an ideal solution, the interactions are there, but they are all energetically identical. Thus in an ideal solution of molecules A and B, A—A and B—B attractions are the same as A—B attractions. This is the case only when the two components are chemically and structurally very similar.
Note that this differs in a fundamental way from the definition of an ideal gas, defined as a hypothetical substance that follows the ideal gas law. The kinetic molecular theory that explains ideal gas behavior assumes that the molecules occupy no space and that intermolecular attractions are totally absent.
The definition of an ideal gas is clearly inapplicable to liquids, whose volumes directly reflect the volumes of their component molecules. And of course, the very ability of the molecules to form a condensed phase is due to the attractive forces between the molecules. So the most we can say about an ideal solution is that the attractions between its all of its molecules are identical — that is, A-type molecules are as strongly attracted to other A molecules as to B-type molecules. Ideal solutions are perfectly democratic: there are no favorites.
Real Solutions
Real solutions are more like real societies, in which some members are "more equal than others."
It should not be surprising molecules as different as benzene and CS2 should interact more strongly with their own kind, hence the positive deviation illustrated here.
Raoult's law, like the ideal gas law, is a limiting law
You will recall that all gases approach ideal behavior as their pressures approach zero. In the same way, as the mole fraction of either component approaches unity, the behavior of the solution approaches ideality. This is a simple consequence of the fact that at these limits, each molecule is surrounded mainly by its own kind, and the few A-B interactions will have little effect. Raoult s law is therefore a limiting law:
it gives the partial pressure of a substance in equilibrium with the solution more and more closely as the mole fraction of that substance approaches unity.
Distillation is a process whereby a mixture of liquids having different vapor pressures is separated into its components.
At first one might think that this would be quite simple: if you have a solution consisting of liquid A that boils at 50°C and liquid B with a boiling point of 90°C, all that would be necessary would be to heat the mixture to some temperature between these two values; this would boil off all the A (whose vapor could then be condensed back into pure liquid A), leaving pure liquid B in the pot. But that overlooks that fact that these liquids will have substantial vapor pressures at all temperatures, not only at their boiling points.
In order to fully understand distillation, we will consider an ideal binary liquid mixture of A and B. If the mole fraction of A in the mixture is XA, then by the definition of mole fraction, that of B is
XB = 1 – XA
Since distillation depends on the different vapor pressures of the components to be separated, let's first consider the vapor pressure vs. composition plots for a hypothetical mixture at some arbitrary temperature at which both liquid and gas phases can exist, depending on the total pressure.
At any given total vapor pressure such as at , the composition of
the vapor in equilibrium with the liquid (designated by xA)
corresponds to the intercept with the diagonal equilibrium line at
. The diagonal line is just an expression of the linearity between vapor
pressure and composition according to Raoult's law.
As before, the intersection of the pressure line
with the
equilibrium curve defines the mole fractions of A and B present in the
vapor. (Note that mole fractions of gases, which we are dealing with
here, are conventionally represented by y, hence yA and yB.)
The curvature of the equilibrium line arises from the need to combine Raoult's law with Dalton's law of partial pressures which applies to gaseous mixtures.
. We can therefore combine them into a single plot, which we show here.
The two liquid-vapor equilibrium lines (one curved, the other straight) now enclose an area in which liquid and vapor can coexist; outside of this region, the mixture will consist entirely of liquid or of vapor.
At this particular pressure , the intercept
with the upper boundary of the two-phase region gives the mole fractions of A and B in the liquid phase, while the intercept
with the lower boundary gives the mole fractions of the two components in the vapor.
Take a moment to study this plot, and to confirm that
- because both intercepts occur on equilibrium lines, they describe the compositions of the liquid and vapor that can simultaneously exist;
- the compositions of the vapor and liquid are not the same;
- in the vapor, the mole fraction of B (the more volatile component of the solution) is greater than that in the liquid;
- in the liquid, the mole fraction of A (the less volatile component) is smaller than that of the vapor.
Hence the very important rule:
The vapor in equilibrium with a solution of two or more liquids is always richer in the more volatile component.
Boiling point diagrams
The rule shown above suggests that if we heat a mixture sufficiently to bring its total vapor pressure into the two-phase region, we will have a means of separating the mixture into two portions which will be enriched in the more volatile and less volatile components respectively. This is the principle on which distillation is based.
But what temperature is required to achieve this? Again, we will spare you the mathematical details, but it is possible to construct a plot similar to the one above except that the vertical axis represents temperature rather than pressure. This kind of plot is called a boiling point diagram. Note especially that:
- The shape of the two-phase region is biconvex, as opposed to the half-convex shape of the pressure-composition plot.
- The slope of the two-phase region is opposite to what we saw in the previous plot, and the areas corresponding to the single-phase regions are reversed. This simply reflects the fact that liquids having a higher vapor pressure boil at lower temperatures, and vice versa.
- The horizontal line that defines the temperature is called the tie line. Its intercepts with the two equilibrium curves specify the composition of the liquid and vapor in equilibrium with the mixture at the given temperature.
- The vapor composition line is also known as the dew point line — the temperature at which condensation begins on cooling.
- The liquid composition line is also called the bubble point line — the temperature at which boiling begins on heating.
The boiling point changes during distillation
The tie line shown above is for one particular temperature. But when we heat a liquid to its boiling point, the composition will change as the more volatile component (B in these examples) is selectively removed as vapor. The remaining liquid will be enriched in the less volatile component, and its boiling point will consequently rise.
In order to understand this process more thoroughly, let us consider the situation at several points during the distillation of an equimolar solution of A and B.
![]() |
![]() |
![]() |
We begin with the liquid at T1, below its boiling point. When the temperature rises to T2, boiling begins and the first vapor (and thus the first drop of condensate) will have the composition y2. |
As the more volatile component B is boiled off, the liquid and vapor/condensate compositions shift to the left (orange arrows). | At T4, the last trace of liquid disappears. The system is now entirely vapor, of composition y4. |
(The right most diagram above is cut off in the print version; it and its caption are reproduced here.) At T4, the last trace of liquid disappears. The system is now entirely vapor, of composition y4.
The principal ideas you should take away from this are that
- distillation can never completely separate two volatile liquids;
- the composition of the vapor and thus of the condensed distillate changes continually as each drop forms, starting at y2 and ending at y4 in this example;
- if the liquid is completely boiled away, the composition of the distillate will be the same as that of the original solution.
Laboratory distillation setup
The apparatus used for a simple laboratory batch distillation is shown here. The purpose of the thermometer is to follow the progress of the distillation; as a rough rule of thumb, the distillation should be stopped when the temperature rises to about half-way between the boiling points of the two pure liquids, which should be at least 20-30 C° apart (if they are closer, then fractional distillation, described below, becomes necessary).
[image]
[link]
Condensers are available in a number of types. The simple Liebig condenser shown above is the cheapest and therefore most commonly used in student laboratories. Several other classic designs increase the surface area separating the vapor/distillate and cooling water, leading to greater heat exchange efficiency and allowing higher throughput. See here for details.
![]() |
![]() |
![]() |
![]() |
Fractional distillation
Although distillation can never achieve complete separation of volatile liquids, it can in principal be carried out in such a way that any desired degree of separation can be achieved if the solution behaves ideally and one is willing to go to the trouble.
The general procedure is to distill only a fraction of the liquid, the smaller the better. The condensate, now enriched in the more volatile component, is then collected and re-distilled (again, only a small fraction), thus obtaining a condensate even-more-enriched in the more volatile component. If we repeat this sequence many times, we can eventually obtain almost-pure, if minute, samples of the two components.
The lever rule
But since this would hardly be practical, there is a better way. In order to understand it, you need to know about the lever rule, which provides a simple way of determining the relative quantities (not just the compositions) of two phases in equilibrium.
The lever rule is easily derived from Raoult's and Dalton's laws, but we will simply illustrate it by example.
The plot shows the boiling point diagram of a simple binary mixture of composition . At the temperature corresponding to the tie line, the composition of the liquid corresponds to
and that of the vapor to
.
So now for the lever rule: the relative quantities of the liquid and the vapor we identified above are given by the lengths of the tie-line segments labeled a and b. Thus in this particular example, in which b is about four times longer than a, we can say that the mole ratio of vapor (of composition ) to liquid (composition
) is 4.
Anatomy of a fractional distillation
As we explained above, it is not practical to carry out an almost-infinite number of distillation steps to obtain nearly-infinitesimal quantities of the two pure liquids we wish to separate. So instead of collecting each drop of condensate and re-distilling it, we will distill half of the mixture in each step.
Suppose you want to separate a liquid mixture composed of 20 mole-% B and 80 mole-% A, with A being the more volatile.
, the first vapor is formed at T0 and has the composition y0, found by extending the horizontal dashed line until it meets the vapor curve. This vapor is clearly enriched in B; if it is condensed, the resulting liquid will have a mole fraction xB approaching that of A in the original liquid.
But this is only the first drop, we don't want to stop there!
As the liquid continues to boil, the boiling temperature rises. When it reaches T1, we will have boiled away half of the liquid. At this point, the "system" composition (liquid plus vapor) is still the same (
), but is now equally divided between the liquid, which we call "residue" R1, and the condensed vapor, the distillate D1.
How do we know it is equally divided? We have picked T1 so that the tie line is centered on the system concentration, so by the lever rule, R1 and D1 contain equal numbers of moles.
We now take the condensed liquid D1 having the composition
, and distill half of it, obtaining distillate of composition D2.
... and then carry out yet another distillation, this time using D3 as our feedstock.
This may be sufficient for some purposes, but we might wish to do much better, using perhaps 1000 stages instead of just 4. What could be more tedious?
Fractionation with reflux
Not to worry! The multiple successive distillations can be carried out
"virtually" by inserting a fractionating column between the boiling flask and the condenser.
These columns are made with indentations or are filled with materials that provide a large surface area extending through the vertical temperature gradient (higher temperature near the bottom, lower temperature at the top.) The idea is that hot vapors condense at various levels in the column and the resulting liquid drips down (refluxes) to a lower level where it is vaporized, which corresponds roughly to a re-distillation.
Vigreux columns having multiple indentations are widely used (above right). Simple columns can be made by filling a glass tube with beads, short glass tubes, or even stainless steel kitchen-type scouring pads. More elaborate ones have spinning steel ribbons.
Separation efficiency: theoretical plates
The operation of fractionating columns can best be understood by reference to a bubble-cap column. The one shown here consists of four sections, or "plates" through which hot vapors rise and bubble up through pools of condensate that collect on each plate. The intimate contact between vapor and liquid promotes equilibration and re-distillation at successively higher temperatures at each higher plate in the column.
Unlike the case of the step-wise fractional distillation we discussed above, none of the intermediate residues is thrown away; they simply drip down back into the pot where their fractionation journey begins again, always leading to a further concentration of the less-volatile component in the remaining liquid.
At the same time, the vapor emerging from the top plate (5) provides a continuing flow of volatile-enriched condensate, although in diminishing quantities as it is depleted in the boiling pot.
If complete equilibrium is attained between the liquid and vapor at each stage, then we can describe the system illustrated above as providing "five theoretical plates" of separation (remember that the pot represents the first theoretical plate.)
Reflux ratio can be adjusted by placing a special control head on top of the fractionation column. The laboratory-type device shown here illustrates the general concept. Reflux control is mainly of importance in large-scale industrial operations.
Some of the more advanced laboratory-type devices (such as some spinning-steel band columns) are said to offer up to around 200 theoretical plates of separating power.
The boiling point diagrams presented in the foregoing section apply to solutions that behave in a reasonably ideal manner — that is, to solutions that do not deviate too far from Raoult's law. As we explained above, mixtures of liquids whose intermolecular interactions are widely different do not behave ideally, and may be impossible to separate by ordinary distillation. The reason for this is that under certain conditions, the compositions of the liquid and of the vapor in equilibrium with it become identical, precluding any further separation. These cross-over points appear as "kinks" in the boiling point diagrams.
High- and low-boiling azeotropes
or
bring the distillation closer to the azeotropic composition indicated by the dashed vertical line. Once this point is reached, further distillation simply yields more of the same "high-boiling" azeotrope.
High- and low-boiling azeotropes are commonly referred to as constant-boiling mixtures, and they are more common than most people think.
"Breaking" an azeotrope
There are four general ways of dealing with azeotropes. The first two of these are known collectively as azeotropic distillation.
- Addition of a third substance that alters the intermolecular attractions is the most common trick. The drawback is that another procedure is usually needed to remove this other substance.
- Pressure-swing distillation takes advantage of the fact that boiling point (T,X) diagrams are two-dimensional slices of a (T,X,P) diagram in which the pressure is the third variable. This means that the azeotropic composition depends on the pressure, so distillation at some pressure other than 1 atm may allow one to "jump" the azeotrope.
- Use of a molecular sieve — a porous material that selectively absorbs one of the liquids, most commonly water when the latter is present at a low concentration.
- Give up. It often happens that the azeotropic composition is sufficiently useful that it's not ordinarily worth the trouble of obtaining a more pure product. This accounts for the concentrations of many commercial chemicals such as mineral acids.
mixture | azeotrope |
---|---|
Ethanol | 98%, high, 78.1°C |
Hydrochloric acid | 20.2% high, 108.6°C |
Hydrofluoric acid | 35.6%, 111.3°C |
Nitric acid | 68%, 120.5°C |
Sulfuric acid | 98.3%, 338°C |
Distillation of ethanol
Ethanol is one of the major industrial chemicals, and is of course the essential component of beverages that have been a part of civilization throughout recorded history. Most ethanol is produced by fermentation of the starch present in food grains, or of sugars formed by the enzymatic degradation of cellulose. Because ethanol is toxic to the organisms whose enzymes mediate the fermentation process, the ethanol concentration in the fermented mixture is usually limited to about 15%. The liquid phase of the mixture is then separated and distilled.
For applications requiring anhydrous ethanol ("absolute ethanol "), the most common method is the use of zeolite-based molecular sieves to absorb the remaining water. Addition of benzene can break the azeotrope, and this was the most common production method in earlier years. For certain critical uses where the purest ethanol is required, it is synthesized directly from ethylene.
Here be briefly discuss two distillation methods that students are likely to encounter in more advanced organic lab courses.
Vacuum distillation
Many organic substances become unstable at high temperatures, tending to decompose, polymerize or react with other substances at temperatures around 200° C or higher.
A liquid will boil when its vapor pressure becomes equal to the pressure of the gas above it, which is ordinarily that of the atmosphere. If this pressure is reduced, boiling can take place at a lower temperature. (Even pure water will boil at room temperature under a partial vacuum.)
Vacuum distillation is very commonly carried out in the laboratory and will be familiar to students who take more advanced organic lab courses. It is also sometimes employed on a large industrial scale.
[source] (vacuum connection at lower right) |
The vacuum distillation setup is similar that employed in ordinary distillation, with a few additions:
- The vacuum line is connected to the bent adaptor above the receiving flask.
- In order to avoid uneven boiling and superheating ("bumping"), the boiling flask is usually provided with a fine capillary ("ebulliator") through which an air leak produces bubbles that nucleate the boiling liquid.
- The vacuum is usually supplied by a mechanical pump, or less commonly by a water aspirator or a "house vacuum" line.
- The boiling flask is preferably heated by a water- or steam bath, which provides more efficient heat transfer to the flask and avoids localized overheating. Prior to about 1960, open flames were commonly used in student laboratories, resulting in occasional fires that enlivened the afternoon but detracted from the student's lab marks.
A Claisen-type distillation head (right) provides a convenient means of accessing the boiling flask for inserting an air leak capillary or introducing additional liquid through a separatory funnel. This Claisen-Vigreux head includes a fractionation column.
Steam distillation
Strictly speaking, this topic does not belong in this unit, since steam distillation is used to separate immiscible liquids rather than solutions. But because immiscible liquid mixtures are not treated in elementary courses, we present a brief description of steam distillation here for the benefit of students who may encounter it in an organic lab course.
A mixture of immiscible liquids will boil when their combined vapor pressures reach atmospheric pressure. This combined vapor pressure is just the sum of the vapor pressures of each liquid individually, and is independent of the quantities of each phase present.
[image]
Because water boils at 100° C, a mixture of water and an immiscible liquid (an "oil"), even one that has a high boiling point, is guaranteed to boil below 100°, so this method is especially valuable for separating high boiling liquids from mixtures containing non-volatile impurities. Of course the water-oil mixture in the receiving flask must itself be separated, but this is usually easily accomplished by means of a separatory funnel since their densities are ordinarily different.
The detailed theory of steam distillation is usually covered in physical chemistry courses and in books that specifically treat distillation.
There is a catch, however: the lower the vapor pressure of the oil, the greater is the quantity of water that co-distills with it. This is the reason for using steam: it provides a source of water able to continually restore that which is lost from the boiling flask. Steam distillation from a water-oil mixture without the introduction of additional steam will also work, and is actually used for some special purposes, but the yield of product will be very limited.
Steam distillation is widely used in industries such as petroleum refining (where it is often called "steam stripping") and in the flavors-and-perfumes industry for the isolation of essential oils.
The term essential oil refers to the aromas ("essences") of these [mostly simple] organic liquids which occur naturally in plants, from which they are isolated by steam distillation or solvent extraction. Steam distillation was invented in the 13th Century by Ibn al-Baiter, one of the greatest of the scientists and physicians of the Islamic Golden Age in Andalusia.
Distillation is one of the major "unit operations" of the chemical process industries, especially those connected with petroleum and biofuel refining, liquid air separation, and brewing. Laboratory distillations are typically batch operations and employ relatively simple fractionating columns to obtain a pure product. In contrast, industrial distillations are most often designed to produce mixtures having a desired boiling range rather than pure products.
Industrial operations commonly employ bubble-cap fractionating columns (seldom seen in laboratories), although packed columns are sometimes used.
Perhaps the most distinctive feature of large scale industrial distillations is that they usually operate on a continuous basis in which the preheated crude mixture is preheated in a furnace and fed into the fractionating column at some intermediate point. A reboiler unit maintains the bottom temperature at a constant value.
[images: Wikimedia Commons]
The higher-boiling components then move down to a level at which they vaporize, while the lighter (lower-boiling) material moves upward to condense at an appropriate point.
Crude oil distillation and refining
Petroleum
Petroleum is a complex mixture of many types of organic molecules, mostly hydrocarbons, that were formed by the effects of heat and pressure on plant materials (mostly algae) that grew in regions that the earth's tectonic movements buried over periods of millions of years. This mixture of liquid and gases migrates up through porous rock until it s trapped by an impermeable layer of sedimentary rock. The molecular composition of crude oil (the liquid fraction of petroleum) is highly variable, although its overall elemental makeup generally reflects that of typical plants.
element | ||||||
---|---|---|---|---|---|---|
amount |
The principal molecular constituents of crude oil are
- alkanes
- Also known as paraffins, these are saturated linear- or branched-chain molecules having the general formula CnH2n+2 in which n is mostly between 5 and 40.
- unsaturated aliphatic
- Linear- or branched chain molecules containing one or more double or triple bonds (alkenes or alkynes).
- Cycloalkanes
- Also known as naphthenes, these are saturated hydrocarbons CnH2n containing one or more ring structures.
- Aromatic hydrocarbons
- These contain one or more fused benzene rings CnHn, often with hydrocarbon side-chains.
Distillation
The first major step of refining is to fractionate the crude oil into various boiling ranges:
The word gasoline predates its use as a motor fuel; it was first used as a topical medicine to rid people of head lice, and to remove grease spots and stains from clothing.
boiling range | fraction name | further processing |
---|---|---|
<30° C | butane and propane | gas processing |
30 - 210° | straight-run gasoline | blending into motor gasoline |
100 - 200° | naphtha | reforming into gasoline components |
150 - 250° | kerosene | jet fuel blending |
160 -400° | light gas oil | distillate fuel blending into diesel or fuel oil |
315 - 540° | heavy gas oil | catalytic cracking: large molecules are broken up into smaller ones and recycled |
>450° | asphalts, bottoms | may be vacuum-distilled into more fractions |
Further processing and blending
About 16% of crude oil is diverted to the petrochemical industry where it is used to make ethylene and other feedstocks for plastics and similar products.
Because the fraction of straight-run gasoline is inadequate to meet demand, some of the lighter fractions undergo reforming and the heavier ones cracking and are recycled into the gasoline stream. These processes necessitate a great amount of recycling and blending, into which must be built a considerable amount of flexibility in order to meet seasonal needs (more volatile gasolines and heating fuel oil in winter, more total gasoline volumes in the summer.)
[image]
Distillation in history: timeline
A good review of the history of laboratory distillation can be found in Chapter 2 of this Google Books version of Erich Krell's 1981 Handbook of Laboratory Distillation.
3600 BCE | Earliest evidence of distillation equipment, found in Mesopotamia |
200 CE | Distillation of water first described by Alexander of Aphrodisias | ~800 | Arabic alchemist and "father of chemistry" Abu Musa Jabir ibn Hayyan (known in the West as Geber) originates several distillation processes and apparatus for carrying them out. (See also here) |
~1000 | Steam distillation invented by Islamic/Andalusian botanist and physician Ibn al-Baiter, who isolated many plant fragrances such as rosewater. |
~1200 | Metallic zinc (bp 907°C) refined in India by distillation |
~1300 | First clear evidence of the distillation of alcohol, in Salerno, Italy. But the ancient Chinese were probably there long before this! |
~1500 | Fractional distillation developed by Tadeo Alderotti |
1500 | First book on distillation published by the German alchemist Hieronymus Braunschweig |
1770 | First published account of distillation of sea water - to obtain drinking water for Royal Navy ships |
1855 | Abraham Gasner, Canadian physician and geologist, patents process for distilling kerosene from bituminous shale. |
1856-57 | World's first large oil refinery opens in Romania |
1878 | François-Marie Raoult (1830 - 1901) publishes the first in a series of work on the freezing points of solutions that eventually led to Raoult's law. |
Gallery
Refinery control then and now

now... [link]
A modern refinery consists of a large variety of processes whose operations must be carefully monitored and coordinated. Prior to the 1960's, control of the hundreds of valves, pumps, temperatures and pressures was accomplished through the use of pneumatic (compressed air) indicators and actuators. Since that time, direct digital control has greatly simplified the task.
Distillation, old and current
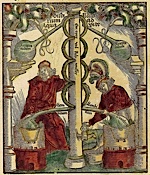
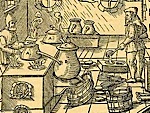
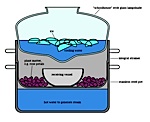
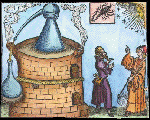
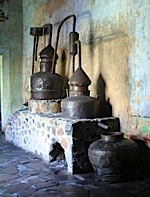
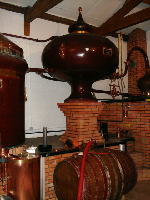
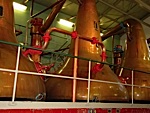
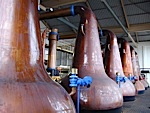